Plastic Express : Delivering Safety Using Cutting-Edge Technology
COO Brian Loft & AVP David Edgarton talk about the use of tech and Plastic Express' unique company culture
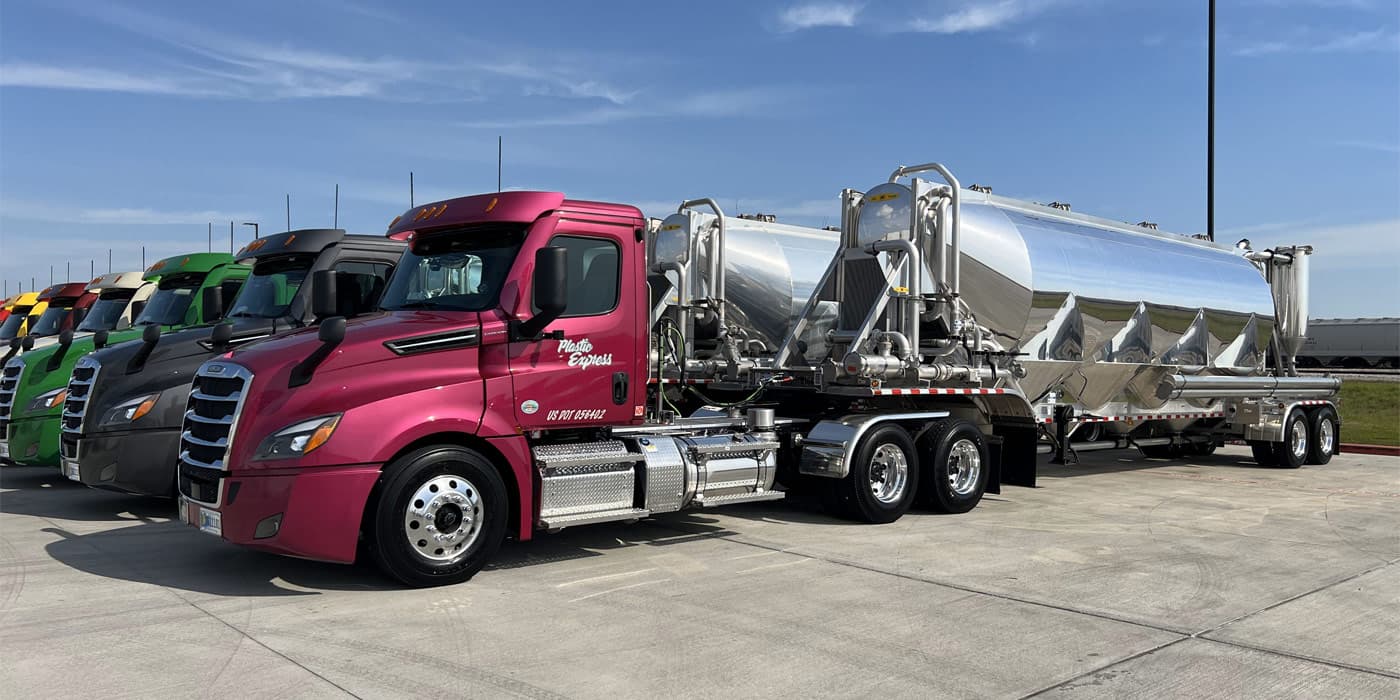
At Plastic Express, safety isn’t just a protocol, it’s a cast-iron promise. The unseen thread that connects their fleet of trucks on the highway to the bustling warehouses they manage. This is a company where tradition meets technology, where growth is measured not only in square footage, revenue and fleet size - but in trust and care. By blending cutting-edge innovation with deeply rooted values, Plastic Express has crafted a story of resilience and ambition in an ever-evolving industry.
The American Executive had the pleasure to speak with Brian Loft, Chief Operating Officer and David Edgarton, AVP of Environment, Health & Safety, and, to discuss Plastic Express’s journey, their innovative safety initiatives, and their ambitious goals for the future. Leadership Rooted in Experience
Leadership at Plastic Express is shaped by a blend of hands-on experience and structured discipline. Brian Loft’s journey with the company began in 1999, when he took on an entry-level role and worked his way up to COO. His deep familiarity with nearly every aspect of the business—from dispatching trucks to managing packaging machines—gives him an authentic, ground-up perspective on operations.
“I’ve worked every job in this company—from sweeping floors to overseeing logistics,” Loft shared. His extensive hands-on experience allows him to lead with credibility and ensure that employees at every level feel valued and understood.
David Edgarton, meanwhile, brings a systems-driven approach to leadership, shaped by his 21-year career as a jet navigator in the U.S. Navy. His military background instilled in him the discipline and decisiveness required for managing safety in high-stakes environments.
“The key is knowing how much time you have to make a decision,” Edgarton explained, reflecting on his transition from aviation safety to logistics. His expertise in compliance programs and structured processes has reinforced a strong safety culture at Plastic Express.
Together, Loft’s operational insight and Edgarton’s strategic mindset create a leadership dynamic that drives the company’s success. Their complementary styles exemplify leadership by example, a core principle embedded in Plastic Express’s ethos.
Building a Culture Around Core Values
At the heart of Plastic Express is its I-ACT values: Integrity, Agility, Care, and Trust. These principles were formalized by the Executive Team several years ago to enforce and document what they felt were the company’s greatest attributes and laid out the Corporate DNA that would move them into the future. This year, the company added “Safe” to its core values, creating the I-ACT-Safe initiative, which emphasizes the importance of safety in all aspects of the company’s operations. “Our core values aren’t just for show,” Loft explained. “They’re about building a culture where our employees feel empowered to prioritize safety.”
The initiative has been transformative. Employees are not just encouraged but empowered to make safety a personal responsibility. From drivers on the road to warehouse staff, everyone is expected to embody the values of I-ACT-Safe. This cultural shift is further reinforced through training programs, communication from leadership, and practical tools that make safety more accessible.
Edgarton noted that the initiative includes three tenets of personal safety: empowerment to slow down, empowerment to stop work, and adherence to responsibility. These principles are designed to give employees the confidence to prioritize safety in their day-to-day tasks, regardless of external pressures.
Embracing Technology for Safety and Efficiency Plastic Express has embraced technology as a cornerstone of its operations. An exciting recent initiative saw them partnering with companies like Netradyne, Geotab, and Gridline Analytics. The goal? Further enhancing safety and efficiency.
Netradyne: Harnessing AI for Safer Roads
Firstly, the Netradyne Driver•i app and GreenZone® Score allows Plastic Express to utilize AI-powered cameras to analyze driving behavior and provide actionable feedback. With cameras offering a 330-degree view, these systems monitor factors like lane changes, hard braking, and speeding. Drivers can view their performance through the app, while managers use the data for coaching and trend analysis. David speaks warmly about the relationship and enthusiastically about the technology:
“These systems give us leading indicators, enabling us to make proactive decisions,” Edgarton explained. “We’ve even integrated financial incentives based on GreenZone scores to encourage safe driving.”
The results speak for themselves. In just six months, the company saw a 13% reduction in severe driving alerts. This improvement not only enhances driver safety but also bolsters customer satisfaction through more reliable and efficient service. Geotab: Real-Time Fleet Management
Next, Geotab’s systems have revolutionized fleet management at Plastic Express. By providing real-time data on vehicle location, driver hours, and vehicle diagnostics, Geotab enables the company to monitor and optimize its fleet’s performance. This data ensures compliance with federal regulations, such as hours-of-service requirements, while also uncovering opportunities to improve efficiency.
“We’ve turned federally mandated programs into tools for growth and safety,” Loft furthers. The Geotab platform also supports digital vehicle inspections, allowing Plastic Express to identify and address maintenance issues quickly, ensuring that its fleet operates safely and efficiently. Gridline Analytics: Comprehensive Insights
Finally, Gridline Analytics complements Geotab by consolidating fleet data into a comprehensive, user-friendly platform. Information means nothing without correct interpretation. By integrating metrics from various sources, Gridline offers a holistic view of driver performance and vehicle operations. This enhanced visibility enables managers to identify trends, address potential safety concerns, and optimize operations at both the terminal and individual driver levels. With all of this technology working in unison, these partnerships have proven pivotal in achieving safety and efficiency goals for Plastic Express. “Gridline gives us the tools to see the bigger picture and make informed decisions,” Edgarton said. This integration of technology and analytics is central to the company’s commitment to continuous improvement.
Overcoming Challenges with Collaboration
Implementing advanced technologies like Netradyne’s cameras and Geotab’s systems required careful planning and clear communication with employees - especially drivers, who initially expressed concerns about privacy. Certainly, a sentiment not without foundation in other companies experiences.
“We were worried we’d lose drivers over the introduction of driver-facing cameras,” Loft admitted. “But we focused on framing it as a tool for improvement rather than surveillance.” Musing that many drivers harbor a slightly nomadic personality type, it’s an understandable issue to focus on.
The company’s approach paid off. By emphasizing the positive aspects of the technology and integrating it gradually, Plastic Express avoided the workforce disruptions that plagued other companies in the industry. Today, drivers see the system as a valuable resource that supports their safety rather than undermining their autonomy.
Not only that, but there is good reason to think the cameras have actually improved staff relationships. With incentives, prizes and recognition for the highest safety scores, we’d wager some members of the team may be more upset with a broken camera than a snapped fan belt! This collaborative mindset extends to the company’s relationships with its technology partners. Edgarton fondly recalls attending the Geotab Connect conference early in his tenure, where he worked closely with representatives from Netradyne and Gridline to provide feedback on their systems. “They were genuinely interested in what we had to say and used our input to improve their software,” he said.
A Commitment to Organic Growth
Unlike many of its competitors, Plastic Express has grown 100% organically, avoiding acquisitions and instead building its operations from within. This strategy has allowed the company to maintain a consistent culture and approach across its expanding footprint, which now includes 5 million square feet of warehousing and a nationwide logistics network.
“Our growth has always been about doing things the right way,” Loft explained. “We’ve built our systems, procedures, and culture from scratch, and that consistency is a big part of what makes us successful.”
This emphasis on internal development extends to the company’s workforce. Plastic Express invests heavily in training and development, ensuring that employees at all levels understand the company’s values and expectations. “Before someone learns how to operate a forklift, they learn how we operate as a company,” Loft said. It’s how Brian cut his teeth, appreciating he can’t effectively manage a person if he can’t fully understand their role. We jokingly ask if he could still perform any job in the company… Humbly and with typical good humor, he jokes that he used to be able to and still can do most – but he certainly doesn’t know how to do all functions of our dynamic company today. Innovation Beyond the Road While much of Plastic Express’s recent success has been driven by advancements in fleet safety, the company is also innovating in its warehousing operations. In 2024, it launched a pilot program with Intenseye, an AI-powered platform that analyzes warehouse camera footage to identify unsafe behaviors. “This is about finding leading indicators in the warehouse environment, just as we’ve done on the road,” Edgarton said. “The system uses AI to monitor for over 40 types of unsafe actions, from improper lifting techniques to cluttered walkways.” The pilot program, which spans 23 warehouses, is still in its early stages, but the potential benefits are clear. By proactively identifying risks, the company can prevent incidents before they occur, creating a safer and more efficient work environment.
Looking Ahead: Goals for 2025 and Beyond
As Plastic Express looks to the future, its goals are ambitious but focused. The company plans to expand its network of truck terminals and warehouses, enhance its AI-driven safety systems, and deepen its commitment to employee empowerment.
“Growth for us is about being better, not just bigger,” Loft emphasized. “Our focus is on bottom-line growth and ensuring that our customers receive the best possible service.”
On the safety front, the company aims to embed the principles of I-ACT-Safe even more deeply into its culture. This includes initiatives to empower employees at all levels to take ownership of safety, as well as programs to make safety training more accessible and engaging.
“We want every associate, whether they’re behind the wheel or in a warehouse, to feel confident in their ability to make safe decisions,” Edgarton said.
A Model for Sustainable Success
Plastic Express’s story is one of balance—between tradition and innovation, growth and stability, and technology and human values. By staying true to its core values while embracing the possibilities of AI and other advanced technologies, the company has set a new standard for safety and efficiency in logistics.
As the industry continues to evolve, Plastic Express is well-positioned to lead the way, proving that a commitment to safety, culture, and continuous improvement is the ultimate competitive advantage.